Why Cleanroom Flooring Matters in EV Battery Plants
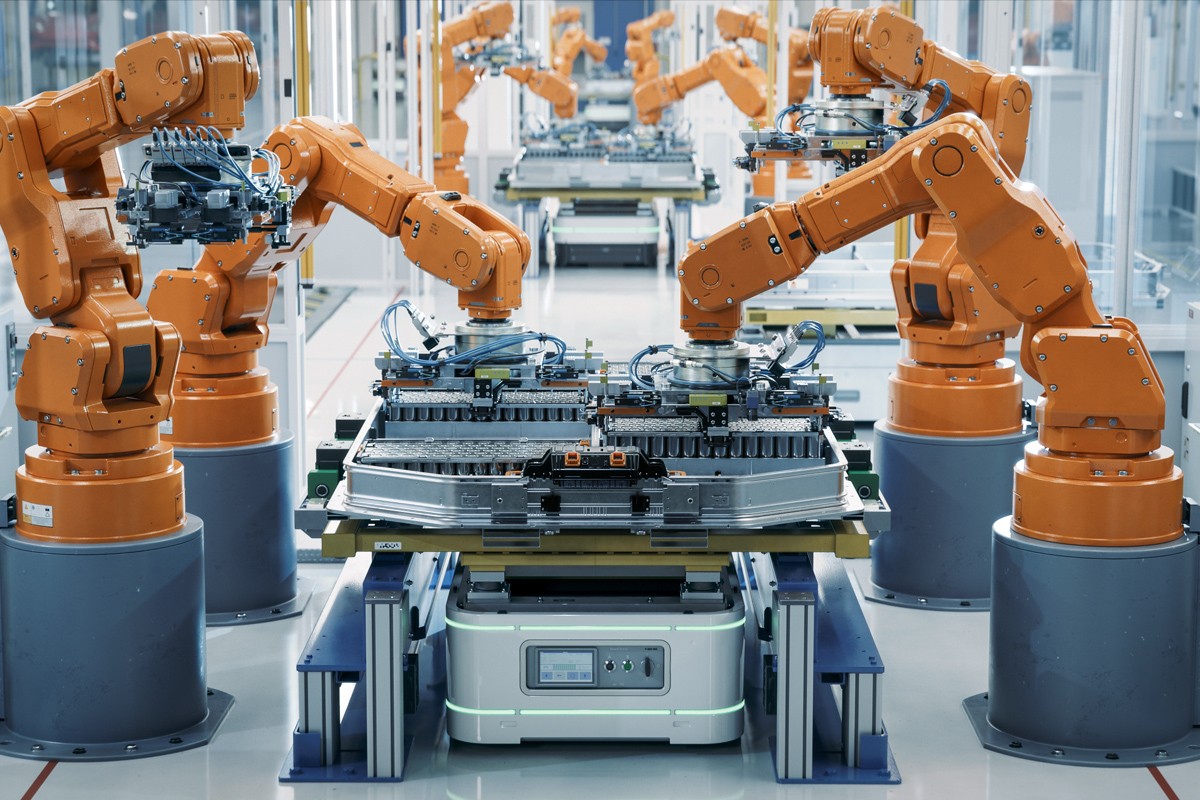
As the world shifts towards more sustainable transportation, electric vehicle (EV) battery plants are becoming central to industrial development. These facilities require ultra-clean environments to maintain product quality, operational safety, and compliance with regulatory standards. While much attention is placed on filtration systems and electrostatic discharge (ESD) protection, flooring often goes under the radar — despite being one of the most critical touchpoints in a cleanroom.
The integration of antimicrobial technology, such as Biomaster, into flooring systems is emerging as a powerful tool to enhance hygiene, reduce contamination risk, and future-proof facilities against microbial threats. When paired with antistatic additives like Staticmaster, these solutions can address both biological and electrostatic hazards — two of the most significant issues in battery production environments.
EV battery production is sensitive to both physical and biological contaminants. Cleanrooms within these facilities are designed to limit particulate intrusion, but bacteria and electrostatic risks such as uncontrolled discharges — can also compromise safety and performance.
Floors are particularly vulnerable due to:
- Heavy foot and trolley traffic
- Occasional chemical spills and electrolyte leaks
- High humidity and static-prone conditions
Conventional flooring materials can become microbial breeding grounds and static charge accumulators. Without built-in product protection, even regular cleaning and grounding procedures may not be enough to ensure compliance.
This is where Biomaster and Staticmaster additives offer a dual-action advantage.
The Role of Biomaster and StaticMaster in Cleanroom Flooring
Biomaster is a silver-ion based antimicrobial additive that can be seamlessly integrated into floor coatings, delivering 24/7 product protection against bacteria. Staticmaster, meanwhile, is an antistatic additive designed to minimise the build-up and discharge of electrostatic energy on treated surfaces — helping to prevent ESD events that could damage sensitive components or ignite flammable substances.
Together, these technologies provide:
- Continuous hygiene assurance between cleaning cycles
- Reduced microbial load
- Electrostatic discharge protection on walking surfaces
- Improved working conditions in dry rooms and assembly areas
- Compliance with both ISO cleanroom classifications and electrostatic safety standards
Key Considerations for Contractors
For contractors working on EV battery facilities, understanding the value of antimicrobial and antistatic flooring is vital to meeting client expectations and certification demands. Four factors should guide flooring system selection:
1. Material Selection and Compatibility
Cleanroom floors must balance mechanical strength with hygiene and static control. Biomaster and Staticmaster can both be added to resin-based coatings — including epoxy and polyurethane systems — without altering their performance characteristics.
These treated surfaces offer:
- Chemical and abrasion resistance
- Seamless, crack-free application
- Built-in antimicrobial product protection
- Integrated static dissipation to help meet ESD control requirements
This makes them ideal for sensitive production zones, electrolyte storage areas, and airlocks where both microbial and electrostatic risks are present.
2. Durability Under Stress
EV cleanrooms are dynamic environments. Forklifts, carts, and foot traffic introduce wear-and-tear, which can create hiding places for bacteria or disrupt static dissipation if left untreated. Biomaster and Staticmaster enhanced floors retain their protective performance even as they age — ensuring long-term integrity.
3. Compliance with Cleanroom and ESD Standards
Battery plants must adhere to ISO 14644 cleanroom classifications and often follow IEC 61340 or equivalent ESD protection standards. Flooring enhanced with Biomaster and Staticmaster helps meet both — making it easier to pass audits and reduce risk.
4. Ease of Installation
These additives are integrated at the manufacturing stage, so they don’t require special handling, additional curing time, or installation changes. Contractors can easily specify flooring systems that offer both antimicrobial and antistatic protection — without compromising deadlines.
Strategic Advantages for OEMs and Facility Owners
Investing in dual-protection flooring offers both immediate and long-term value:
- Risk Mitigation: Reduce the potential for microbial and electrostatic issues before they affect operations or certification
- Cost Savings: Reduce downtime due to contamination, ESD incidents, or flooring failures
- Compliance Confidence: Meet hygiene and static control benchmarks across departments
- Sustainability: Extend flooring lifespan
- Reputation: Demonstrate a commitment to innovation, and best practices
Looking Ahead
As EV battery technology evolves, so too must the environments in which it’s produced. Flooring should no longer be seen as just a structural necessity — it is a frontline defence against microbial contamination and electrostatic discharge in mission-critical facilities.
By incorporating Biomaster and Staticmaster additives into flooring systems, contractors and manufacturers can enhance product performance, support regulatory compliance, and ensure cleanroom environments are fit for the future of mobility.
What Next?
🔗 Follow us on Social Media, here is our LINK TREE
✉️ See how our additive technology can benefit your business by CONTACTING US
🦠 Find out more about Biomaster Antimicrobial Technology HERE
🎥 Watch our video on how Biomaster works WATCH NOW
📰 Subscribe to our Newsletter - SUBSCRIBE
← Back to blog